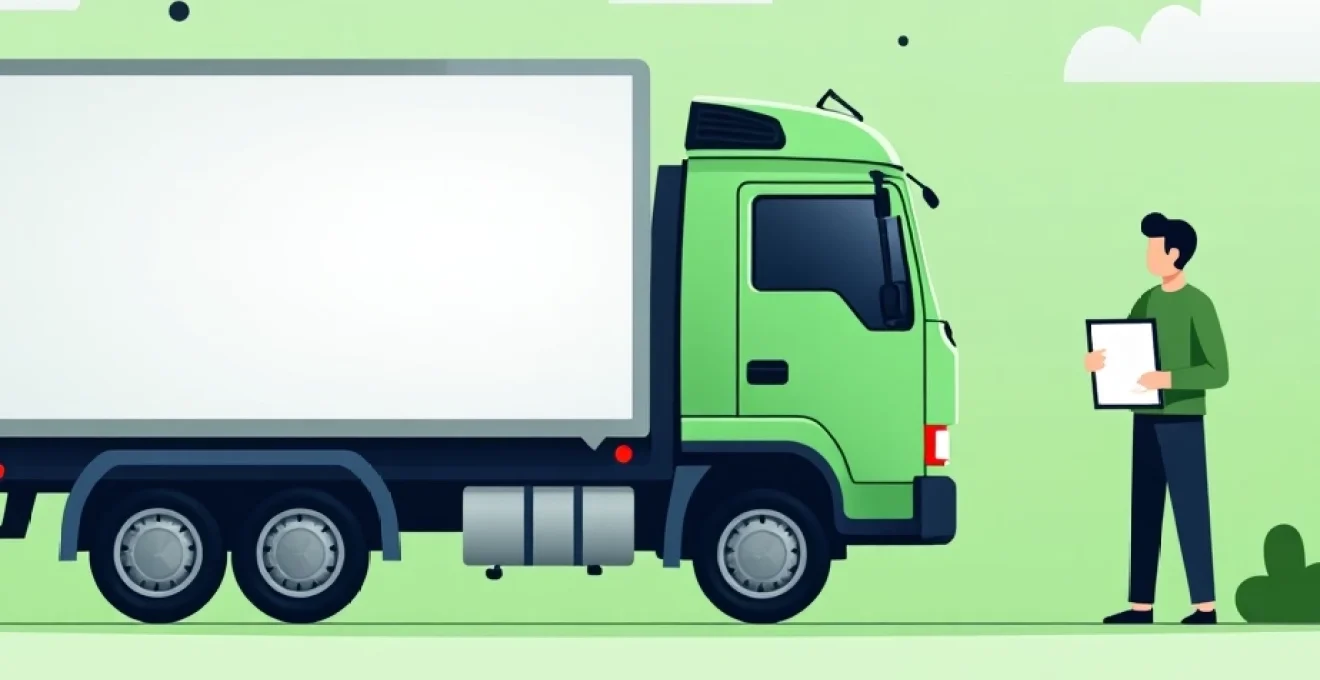
In today's competitive business landscape, fleet maintenance plays a pivotal role in driving operational success. As organizations rely heavily on their vehicle fleets for transportation, delivery, and service provision, the importance of a well-maintained fleet cannot be overstated. Effective fleet maintenance not only ensures the longevity and reliability of vehicles but also significantly impacts cost efficiency, safety compliance, and environmental sustainability. By implementing robust maintenance strategies and leveraging cutting-edge technologies, companies can optimize their fleet operations, reduce downtime, and ultimately enhance their bottom line.
Preventive maintenance strategies for fleet longevity
Preventive maintenance is the cornerstone of any successful fleet management program. By adopting a proactive approach to vehicle care, you can significantly extend the lifespan of your fleet assets and minimize unexpected breakdowns. Implementing a comprehensive preventive maintenance strategy involves scheduling regular inspections, servicing, and repairs based on manufacturer recommendations and historical data.
One effective preventive maintenance technique is to establish a tiered maintenance schedule. This approach involves categorizing maintenance tasks based on their frequency and complexity. For instance, you might schedule oil changes and tire rotations more frequently than transmission flushes or brake system overhauls. By stratifying maintenance tasks, you can ensure that each vehicle receives the appropriate level of care without overburdening your maintenance team or budget.
Another critical aspect of preventive maintenance is driver education. Encouraging your drivers to perform daily vehicle inspections and report any unusual sounds, vibrations, or performance issues can help catch potential problems early. This collaborative approach to maintenance not only improves vehicle longevity but also fosters a culture of responsibility and care among your fleet operators.
Predictive analytics in fleet maintenance optimization
While preventive maintenance provides a solid foundation, predictive analytics takes fleet maintenance to the next level. By harnessing the power of data and advanced algorithms, predictive maintenance allows you to anticipate potential issues before they occur, further reducing downtime and maintenance costs.
Machine learning algorithms for failure prediction
Machine learning algorithms play a crucial role in predictive maintenance by analyzing vast amounts of historical and real-time data to identify patterns and predict potential failures. These algorithms can consider multiple variables, such as vehicle age, mileage, operating conditions, and previous maintenance records, to generate accurate predictions of when a component is likely to fail.
For example, a machine learning model might analyze engine performance data and predict that a particular vehicle's alternator is likely to fail within the next 500 miles. This insight allows you to schedule maintenance proactively, avoiding unexpected breakdowns and minimizing disruptions to your operations.
Iot sensors and real-time data collection
The Internet of Things (IoT) has revolutionized fleet maintenance by enabling real-time data collection from vehicles. IoT sensors can monitor various vehicle parameters, such as engine temperature, oil pressure, tire pressure, and battery voltage, providing a continuous stream of data for analysis.
By integrating IoT sensors into your fleet, you can gain unprecedented visibility into the health and performance of your vehicles. This real-time data allows for immediate detection of anomalies and enables your maintenance team to respond quickly to potential issues, often before they manifest as visible problems.
Telematics integration for performance monitoring
Telematics systems play a vital role in modern fleet maintenance by providing comprehensive vehicle performance data. These systems combine GPS technology with onboard diagnostics to offer insights into vehicle location, speed, fuel consumption, and driver behavior. By integrating telematics data into your maintenance strategy, you can identify trends and patterns that may indicate the need for preventive maintenance or driver training.
For instance, telematics data might reveal that certain vehicles consistently experience higher fuel consumption or more frequent brake wear. This information can help you prioritize maintenance tasks and address underlying issues that may be affecting vehicle performance and longevity.
Predictive maintenance software platforms
To effectively leverage predictive analytics in fleet maintenance, many organizations turn to specialized software platforms. These platforms, such as Fleetio and Fiix, offer comprehensive solutions for managing and optimizing fleet maintenance operations. They typically include features like maintenance scheduling, work order management, inventory tracking, and data analytics.
By utilizing these platforms, you can centralize your maintenance data, automate routine tasks, and gain valuable insights into your fleet's performance. The integration of predictive maintenance software can significantly streamline your maintenance processes and help you make data-driven decisions to improve overall fleet efficiency.
Cost-efficiency through effective maintenance management
One of the primary benefits of a well-executed fleet maintenance program is its potential for significant cost savings. By implementing effective maintenance management strategies, you can reduce overall operational costs, extend vehicle lifespans, and optimize resource allocation.
Total cost of ownership (TCO) reduction techniques
Reducing the total cost of ownership for your fleet involves considering all expenses associated with acquiring, operating, and maintaining vehicles throughout their lifecycle. Effective maintenance plays a crucial role in minimizing TCO by preventing costly breakdowns, extending vehicle lifespan, and optimizing fuel efficiency.
One TCO reduction technique is to implement a data-driven replacement strategy. By analyzing maintenance costs, fuel efficiency, and reliability data, you can determine the optimal time to replace vehicles before they become a financial burden. This approach ensures that you maximize the value of each asset while minimizing long-term costs.
Inventory management and parts optimization
Efficient inventory management is essential for controlling maintenance costs and minimizing vehicle downtime. By optimizing your parts inventory, you can ensure that critical components are always available when needed while avoiding the costs associated with overstocking.
Implementing a just-in-time inventory system, coupled with predictive maintenance insights, can help you strike the right balance between parts availability and inventory costs. This approach allows you to maintain a lean inventory while ensuring that you have the necessary parts on hand for scheduled maintenance and predicted repairs.
Labor allocation and technician productivity metrics
Maximizing the productivity of your maintenance team is crucial for cost-efficient fleet management. By tracking technician productivity metrics and optimizing labor allocation, you can ensure that your maintenance resources are used effectively.
Consider implementing a system to track key performance indicators (KPIs) such as average repair time, first-time fix rate, and technician utilization. These metrics can help you identify areas for improvement, provide targeted training, and optimize your maintenance workflow to maximize efficiency.
Compliance and safety: maintenance's role in regulatory adherence
Maintaining a safe and compliant fleet is not just a legal obligation; it's a critical aspect of protecting your drivers, assets, and reputation. Effective maintenance practices play a vital role in ensuring that your fleet meets all relevant safety standards and regulatory requirements.
Regular safety inspections should be an integral part of your maintenance program. These inspections should cover critical components such as brakes, tires, lights, and safety systems. By documenting these inspections and promptly addressing any identified issues, you can demonstrate your commitment to safety and compliance.
Additionally, staying up-to-date with changing regulations is crucial. As environmental and safety standards evolve, your maintenance practices may need to adapt. For example, new emissions regulations may require more frequent maintenance of exhaust systems or the adoption of new technologies to reduce pollutants.
A well-maintained fleet not only ensures operational efficiency but also demonstrates a commitment to safety and regulatory compliance, which can significantly enhance your company's reputation and reduce legal risks.
Environmental impact and sustainability in fleet maintenance
As environmental concerns continue to gain prominence, fleet managers must consider the ecological impact of their maintenance practices. Adopting sustainable maintenance strategies can not only reduce your environmental footprint but also lead to cost savings and improved public perception.
Emissions reduction through proper maintenance practices
Regular maintenance plays a crucial role in minimizing vehicle emissions. Well-maintained engines operate more efficiently, consuming less fuel and producing fewer pollutants. By implementing a rigorous maintenance schedule that includes regular tune-ups, air filter replacements, and emissions system checks, you can significantly reduce your fleet's environmental impact.
Moreover, proactive maintenance can help identify and address issues that may lead to increased emissions, such as faulty oxygen sensors or clogged catalytic converters. By promptly addressing these issues, you can ensure that your vehicles continue to meet or exceed emissions standards throughout their operational life.
Green technologies in fleet maintenance facilities
Incorporating green technologies into your maintenance facilities can further enhance your sustainability efforts. Consider implementing energy-efficient lighting, solar panels, or geothermal heating and cooling systems to reduce energy consumption. Additionally, water recycling systems for vehicle washing and the use of environmentally friendly cleaning products can minimize your facility's environmental impact.
Another area to focus on is waste management. Implementing proper recycling programs for used oil, batteries, and other vehicle components can significantly reduce your maintenance operation's environmental footprint while potentially generating additional revenue streams.
Lifecycle assessment of maintenance products and procedures
Conducting lifecycle assessments of the products and procedures used in your maintenance operations can provide valuable insights into their environmental impact. This analysis can help you identify more sustainable alternatives and optimize your maintenance processes to minimize waste and resource consumption.
For example, you might discover that switching to longer-lasting synthetic oils can reduce the frequency of oil changes, resulting in less waste oil and fewer disposal issues. Similarly, adopting reusable air filters or implementing more efficient parts cleaning methods can reduce both waste and operating costs.
Fleet maintenance technology integration and digital transformation
The digital transformation of fleet maintenance operations has opened up new possibilities for efficiency, accuracy, and cost savings. By integrating advanced technologies into your maintenance processes, you can streamline operations, improve decision-making, and enhance overall fleet performance.
Cloud-based fleet management systems (FMS)
Cloud-based fleet management systems offer a centralized platform for managing all aspects of fleet operations, including maintenance. These systems provide real-time access to vehicle data, maintenance histories, and performance metrics from any device with an internet connection. This accessibility enables faster decision-making and more efficient resource allocation.
Moreover, cloud-based FMS solutions often include features such as automated maintenance scheduling, digital work order management, and integration with other business systems. This level of integration can significantly reduce administrative overhead and improve the accuracy of maintenance records.
Mobile maintenance apps for field service technicians
Mobile maintenance apps have revolutionized the way field service technicians perform their duties. These apps provide technicians with instant access to vehicle histories, repair manuals, and parts inventories, enabling them to diagnose and address issues more quickly and accurately.
Furthermore, mobile apps can streamline the process of recording maintenance activities, capturing photos of vehicle conditions, and updating work orders in real-time. This immediate data capture reduces the risk of errors and ensures that all maintenance activities are properly documented for compliance and analysis purposes.
Blockchain for maintenance record integrity and traceability
Blockchain technology is emerging as a powerful tool for ensuring the integrity and traceability of maintenance records. By creating an immutable, decentralized ledger of all maintenance activities, blockchain can provide an unprecedented level of transparency and trust in fleet maintenance operations.
Implementing blockchain for maintenance record-keeping can help prevent fraud, ensure compliance with regulatory requirements, and simplify the process of transferring vehicle maintenance histories during fleet acquisitions or disposals. While still in its early stages of adoption in the fleet industry, blockchain has the potential to significantly enhance the reliability and value of maintenance data.
As you navigate the complex landscape of fleet maintenance, remember that the key to success lies in adopting a holistic approach that combines preventive strategies, predictive analytics, cost-efficient management, and cutting-edge technologies. By continuously refining your maintenance practices and embracing innovation, you can ensure that your fleet remains a powerful asset driving your organization's operational success.